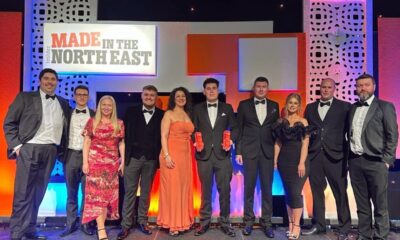
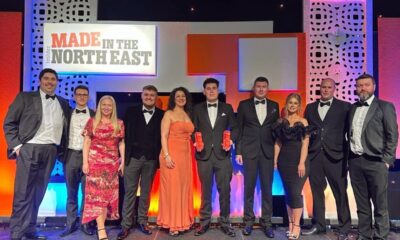
While employees in many industries have had the option to migrate to remote working through the course of the pandemic, the nature of our business at Dyer Engineering (as fabrication specialists) has made this impossible. In order to keep our workforce safe and healthy through 2020 and beyond, we have instead been focused on implementing changes to our processes and procedure to ensure that not only can we continue to trade effectively, but that we can retain our status as leading fabrication specialists.
As a business that stakes our reputation on being problem solvers and early adopters of technology, we’ve been driven to not only survive but thrive through Covid-19. And so our digital team have set about working to ensure that we are finding accurate, reliable and effective solutions to protect our employees and minimise the risk of the disease spreading in the workplace.
Our first steps were, of course, to follow the government guidance for factories, plants and warehouses provided on the www.gov.uk website. This formed the foundation for the many adaptations and changes we have made on-site. From introducing precautions relating to arriving at and leaving work to maintaining hygiene at workstations and workplaces, we’ve been rigorous in our approach to all necessary mitigating actions. However, we also knew that there was more that we could do to protect our employees and the business.
Our Digital Innovation team set to work on this challenge, looking at ways in which the business can utilise technology to safeguard our staff from a potential outbreak. Through close collaboration with our IoT (Internet of Things) technology partner, ThinkInside, we have been able to work together to develop and implement sophisticated PPE (Personal Protective Equipment) trackers that captures and records all “contacts” between team members that are deemed to be within 2 metres for a period of more than 15 minutes. This is in addition to the practical benefits of protective clothing and equipment, which can help prevent transmission of the virus itself.
The benefit of this innovative approach is that we can respond quickly in the event of a positive Covid-19 test and surgically identify those at risk with genuine accuracy. For our workforce, this offers an easy to understand system and peace of mind that the risk of infection is significantly reduced. From a business continuity perspective, it also serves to minimise the number of people who have to self-isolate once a positive test is identified – helping to avoid a total shutdown of a department or production line.
Having worked with the team at ThinkInside to develop and implement our IoT asset tracking solution, we knew how powerful and effective monitoring tools could be in a manufacturing environment. And given the importance of location intelligence through Covid-19, we had no hesitation in working with our colleagues at ThinkInside to create a ThinkIn solution that would help us to develop smart data views and reports to allow the effective utilisation of the captured data in a way the whole business can easily understand and react to.
While much has been made of track and trace technologies on a national scale with the NHS app, we knew that it was essential to implement a solution that was rigorous and accurate within our own work setting – both for the health of our team and the productivity of the business.
Dyer Engineering Head of Digital Innovation, Richard Larder, explains:
“As we adapted swiftly to meet the demands of the ‘new normal’ it became clear that the business had to do more to ensure strict compliance with physical distancing, implement stringent hygiene regulations and track interactions effectively for the sake of our employees’ health. Digital innovation in engineering is nothing new, of course, but it would be fair to say that the restrictions and requirements of the pandemic are fairly unique.
The implementation of the ThinkIN application has given us the functionality we needed to protect our workforce within a short period of time. Now we have real-time data that can be used to keep our team safe and manage risk on a day-to-day basis.”
Wearables and on-person tracking devices are becoming increasingly common, thanks to the likes of Apple watches, Fitbits and other fitness tracking devices. By utilising such technologies in the workplace environment, it is possible to ensure adherence to government guidelines in a frictionless manner.
Richard Larder continues:
“The best technologies are often those that work seamlessly in the background and simply allow individuals to get on with the job at hand. By working closely with our partners at ThinkInside, we’ve been able to do that successfully. Innovations like these will help us to work effectively through the remainder of the pandemic and continue to build on our strong reputation.”
Despite the promising news of a Coronavirus vaccine, it is evident that the “new normal” we find ourselves in will still be here stay for many more months. Until we can safely welcome staff back to work without these precautionary measures, everyone at Dyer Engineering is proud of the progress we have made through 2020 and the agile response we have shown in the face of real adversity.
Throughout the year we have continued to fulfil orders with our customers, and we believe that the hard work put in this year will help us to reach our growth ambitions as we progress into 2021 and beyond.
If you are looking to engage with leading North East fabrication specialists for all of your metal component needs, get in touch with us here.